Is the Construction Industry getting safer?
Although safety improved at the turn of the century, data indicates that safety is no longer improving in Australia.
Data from Safe Work Australia shows a substantial improvement in safety over the past 20 years, by measure of deaths per 100,000 workers.
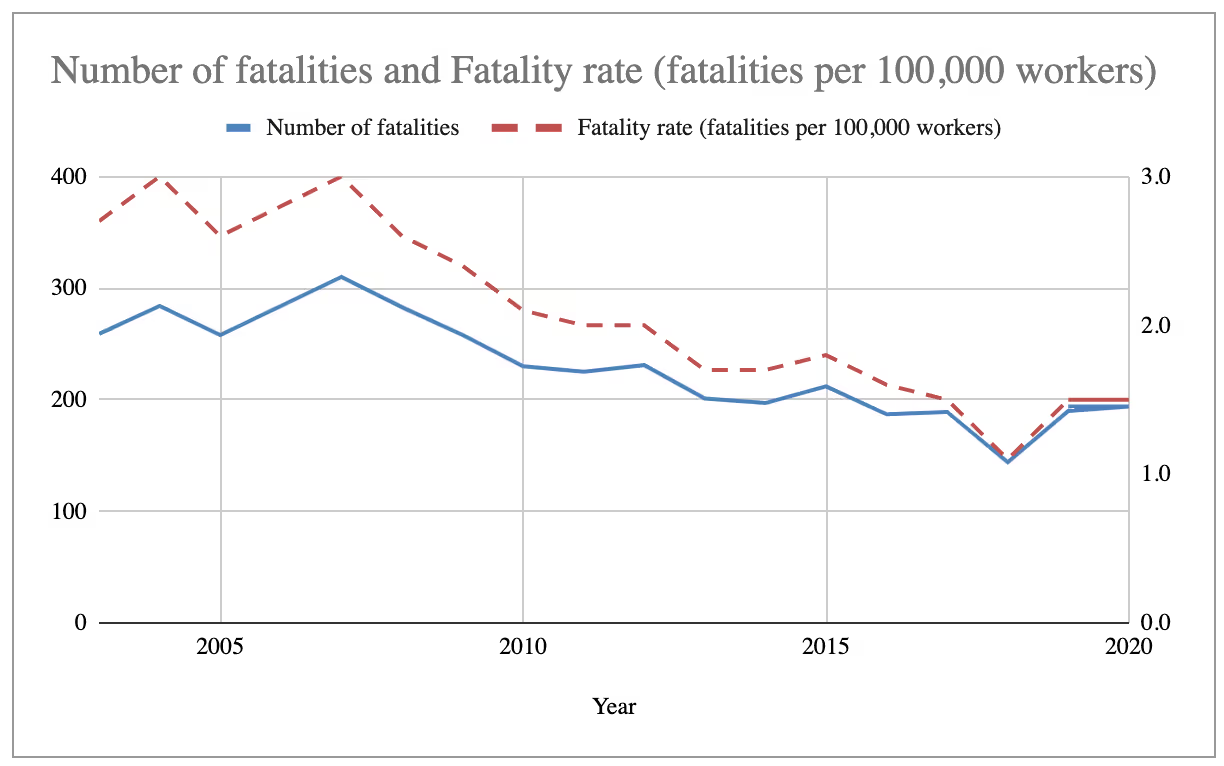
In 2003, the figure was 2.7, and last year the figure had dropped to 1.6, a 37% reduction.
At first blush, a 37% improvement in the worker fatalities seems fantastic.
But let's have a look at the figures averaged over five year periods:
- 2003-2006 – 2.8
- 2007-2010 – 2.5
- 2011-2014 – 1.9
- 2015-2018 – 1.5
- 2019-2022 – 1.5
Changing the resolution of the data to five year averages, we can see that the bulk of the improvements over the past 20 year period were at the start of the period. The past seven years has shown no improvement at all.
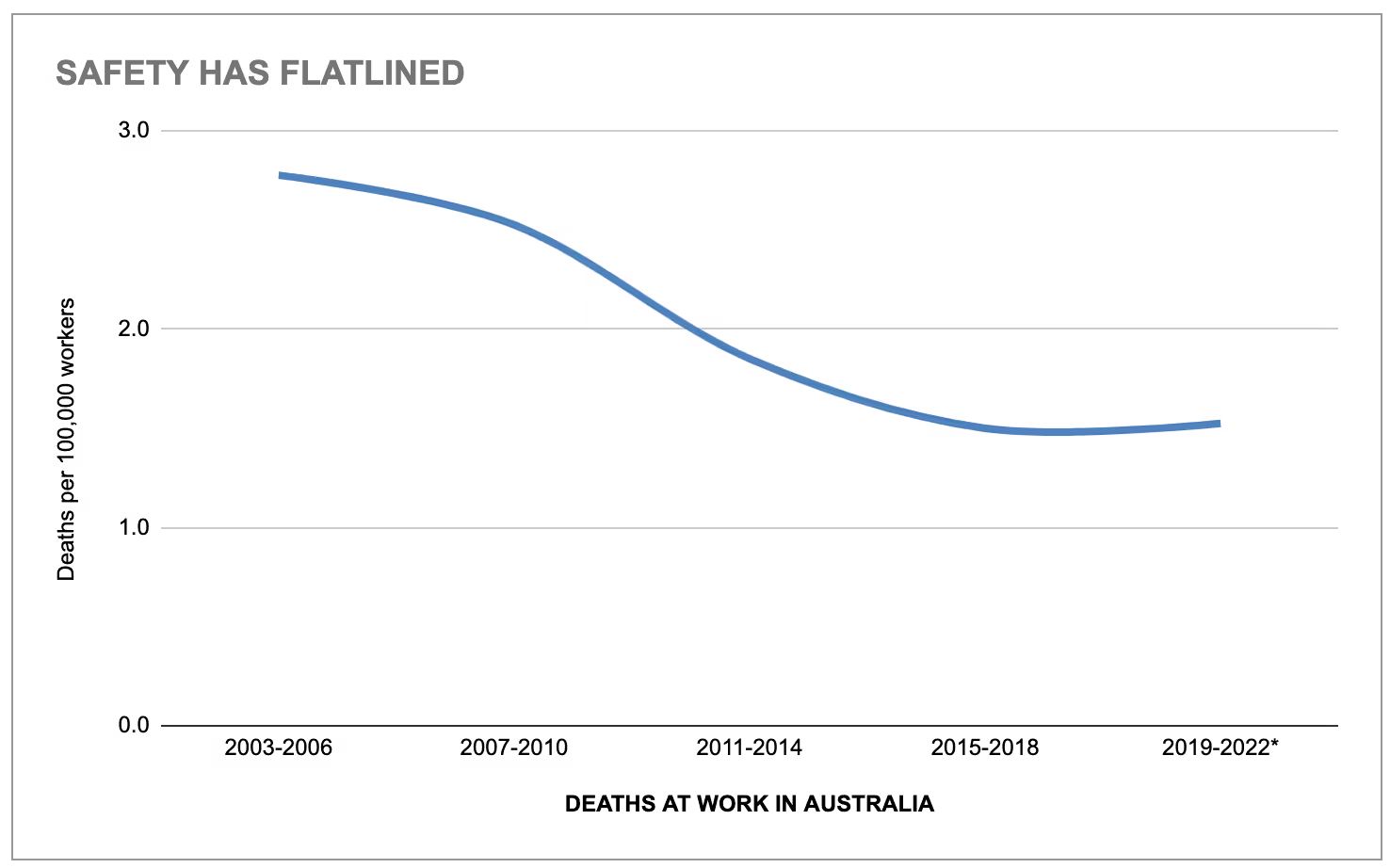
In fact, it can be argued that there has been some regression, especially if you normalise for the Covid year, which showed very few fatalities at work due to people being confined to their homes.
How could safety possibly be going backwards?
How can this be? After all, in the past thirty years, safety in the workplace has gone from being a side issue to being of prime importance. "Safety First" has become cliche. For instance, here are just three rules put in place in the past seven years alone, whose sole purpose was to improve safety, focusing on the construction industry:
- Review of the model WHS Laws 2018
- Transition to ISO 45001
- Gross Negligence as a fault element in the Category 1 offence
With such a focus on safety, and so many new rules and regulations appearing over the past twenty years, how could the safety statistics be getting worse?
Tools and processes can't fix everything
Management consultant McKinsey & Company wrote a paper in 2019 on safety in the workplace. Titled Overcoming limiting mind-sets to improve safety, this paper proposed what has been confirmed by subsequent data: that safety performance tends to plateau after an initial period of improvement.
The cause of this plateau, according to the paper, was an overemphasis on the tools and processes required to manage safety, and an underemphasis on the mindsets of the people working in the organisations.
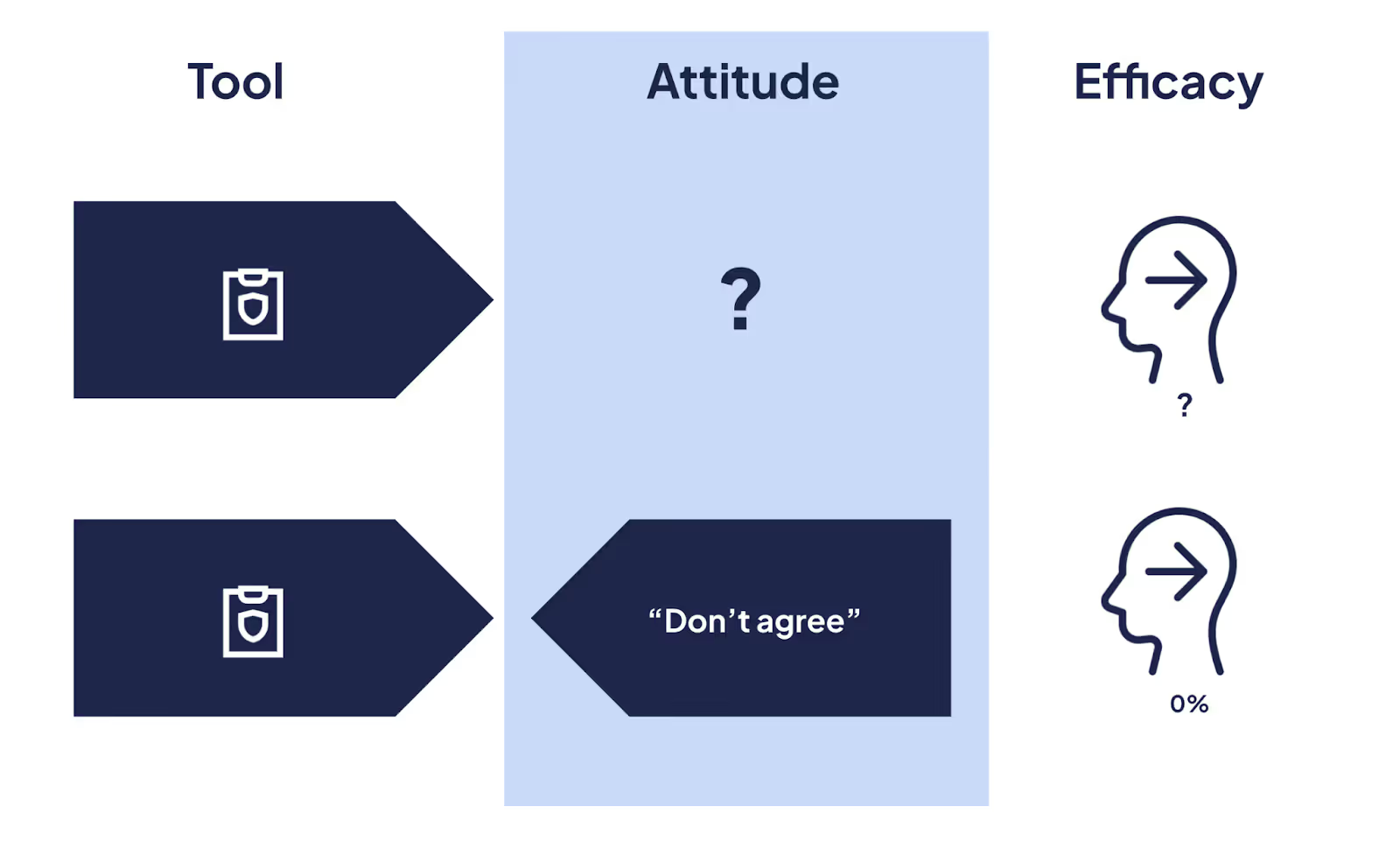
The above diagram shows tools & processes, passing through the filter of the attitude of the user, before looking at efficacy. Tools to date have been designed and expected to just work without considering what the user is thinking.
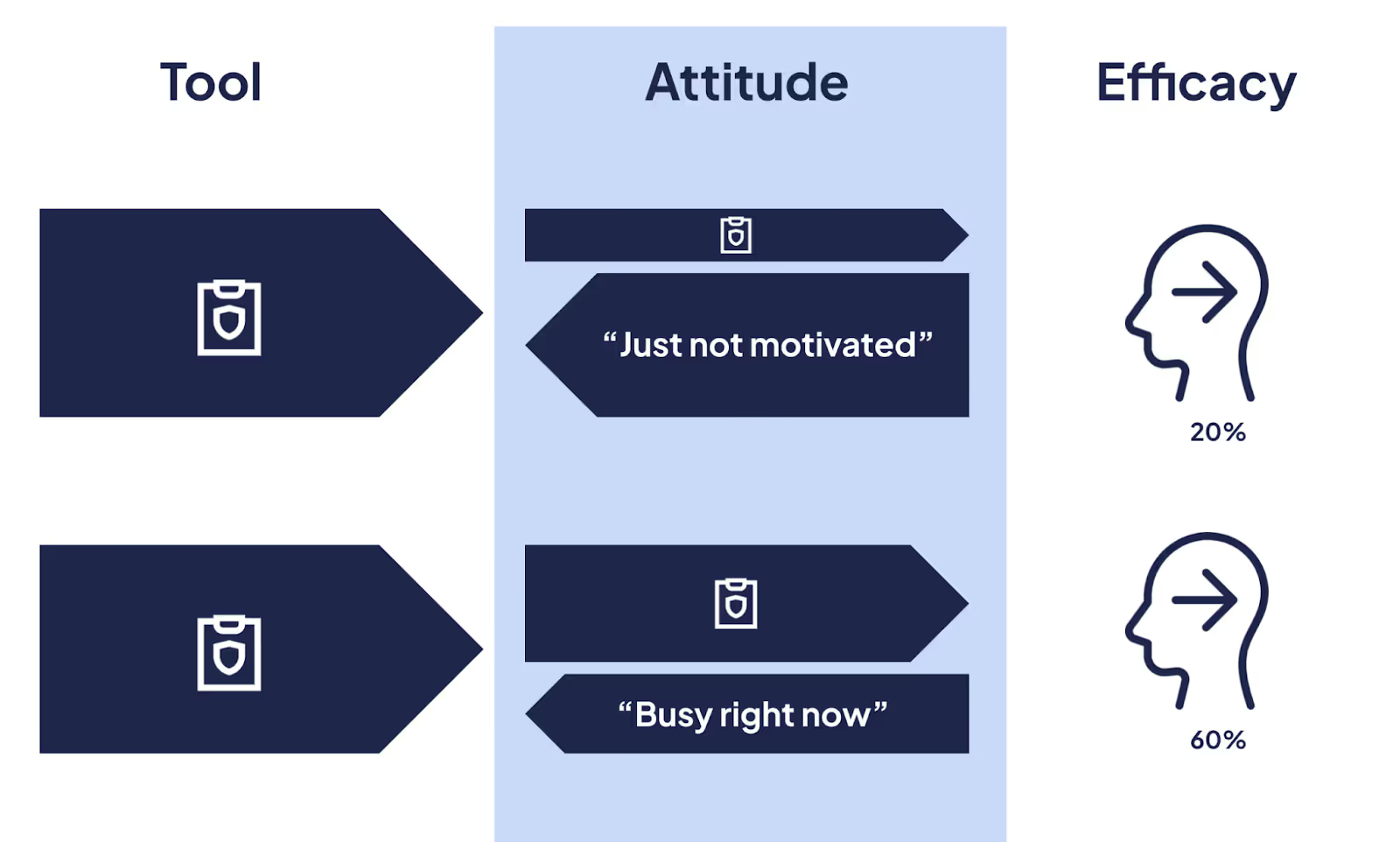
The above diagrams illustrate how if a user is distracted or simply not motivated, then this directly affects the efficacy of the tool itself.
In other words, wherever humans are involved, designing the tool or process is only half the picture. We must consider the attitude of the receiver.
Why couldn’t the safety establishment see this earlier?
Let's say the modern safety era started roughly when the first workplace health & safety laws were promulgated in the 1990s. Back then, as now, construction and mining routinely topped the list of the most dangerous industries. So most of the safety initiatives tended to come out of these industries.
Given both construction and mining are predominantly staffed by engineers (with next to zero psychologists), an engineering approach was taken to improving safety. New forms and processes were created to solve the problem, and measures such as down-time due to an injury, or "lost-time injuries", became the metric by which safety was determined.
This engineering-approach to safety created a compliance mindset, where "perfection" was zero [injuries] and anything else was a form of failure. This became an embedded mindset. In a sense, the entire safety establishment became a slave to this compliance paradigm.
The missing piece
In a post titled The psychology of warnings, Dr Marc Green describes the two-way street that applies to any communication: one is the message itself, and other is the receptivity of the viewer.
Green states that without considering how willing people are to receive a message, an important message may be ineffective. In essence, Green brings academic insight to the idiom "falling on deaf ears".
And this is what the McKinsey paper discovered when reviewing workplace safety. A process-obsessed, compliance based approach had ironically forgotten that people are at the centre of any safety initiatives.
What was the result of all this?
The paper presented five limiting mindsets that were holding back further improvement in safety, including a fear of blame, disempowerment, a trade-off between safety and productivity, a fatalistic mindset and complacency.
When you look at safety in the construction industry today, does any of that sound familiar?
Recommending a way forward
Both the McKinsey and Green papers shared the view that the solution lay in considering the mindsets of people. The McKinsey paper offered four suggestions to improve safety culture through changing mindsets:
- Reward safe behaviours
- Clarify that safety is the priority
- Develop soft skills
- Role model behaviours from the top
How can this be done?
A positive safety approach is entirely in line with the McKinsey recommendations.
First, rewarding safe behaviours sits at the heart of positive safety.
Second, in a capitalist society, monetary rewards provide concrete evidence of intention.
Third, "positive conversations" between worker and supervisor are at the heart of the positive safety model.
And fourth, when management rewards workers for carrying out safety roles, it becomes clear that management is serious.
How can I get my team to approve a pilot?
Let us help you with the benefits of positive safety using Scratchie in summary:
- Surveys show Scratchie improves safety attitudes on sites by around 28%;
- Scratchie reduces the time wasted by supervisors chasing up safety issues – around 1-2 hours per week is saved;
- Morale and mental wellness on site improves – over 95% of workers surveyed prefer to work on sites that have Scratchie;
- Dealflow improves – more and more large asset owners are preferring construction companies who are innovating in safety and mental wellness.
You can download this as a one-pager here.
Scratchie demo
You can click here to book a 15 minute demo with one of our representatives. We will show you how easy it is to get Scratchie started on your project.
References
We thank Dr Marc Green and McKinsey & Co. Here they links to their posts:
https://www.visualexpert.com/Resources/psychwarnings.html